Holocraft
A downloadable hologram generator
Status | In development |
Category | Tool |
Rating | Rated 5.0 out of 5 stars (1 total ratings) |
Author | Deftware |
Tags | 3D, cnc, Generator, hologram, optics, specular-hologram |
Average session | A few minutes |
Languages | English |
Links | Blogger |
Comments
Log in with itch.io to leave a comment.
Do I have to re-buy holocraft to download it now since I cant download it on this site anymore
Has anyone done this on black granite? I'm thinking of use on a gravestone.
I'd like to see how that goes!
Try downloading and installing vc_redist.x64.exe from here: https://www.microsoft.com/en-ca/download/details.aspx?id=48145
Let me know if that fixes the issue for you.
- Charlie
I tried to install vc_redist.x64.exe but it fails, error 0x80070659. I think my pc has problems.
holography
Oh no! Running vcredist installation as administrator might work. Give it a shot and let me know how it goes.
- Charlie
That does't work either, I have tried every thing I can think of. However, v2.2 runs great and is exactly what I have needed for many years, I am really happy to have found your great work. Thank you.
Holography
After doing some more digging it appears that the reliance on vcomp140.dll is entirely because of Holocraft's use of Freeimage library just for loading some images. Holocraft itself does not have this dependency which is why v2.2 works but does not have the texture based optic generation mode working yet. I could re-work the texture optic code to use internal image loading code, or a different library, that does not have the vcomp140.dll dependency and fix the issue. I'm not a fan of requiring users to install things they shouldn't need like the vcredist.exe and if I knew that it was a thing before I used Freeimage.dll I would've not used it at all!
I'm just about to finish launching the new website and am very busy with that but I'll figure something out for v2.4 to get off the vcomp140.dll dependency. I am very sorry for the inconvenience :P Feel free to share any holograms on this forum that you manage to create :)
- Charlie
Hi! It would be fun if we can use textures for background. Even if its an automatic simple background, it would greatly improve the look of the boundaries.
Tom
Hi Tom,
I like the idea but the only thing that comes to mind is how the groove optics destructively interfere with eachother to where they are not reflecting light anymore, and a background will add an entire field of optics over the hologram surface and interfere with the foreground object. I will play with the idea and see if I can come up with something after I finish launching the new Deftware store website over the coming few weeks and releasing the first beta release of PixelCNC.
Thanks for the feedback! :)
- Charlie
Hi, do you have any plans to keep upgrading the Holocraft software?
Best regards,
Dan
Hi Dan,
There's always time to squeeze in new features and functionality for Holocraft - I just don't know what users might be looking for. I do have a few ideas but right now my primary focus is developing and promoting PixelCNC. I'm always motivated by a juicy user request though. If there's anything specific you're looking for or want just let me know and I'll see what I can do :)
complete newbie here. Wondering about feasibility of putting holograms on vinyl records. This would involve creating the image on a lacquer disc...which then would be used to make metal stampers for pressing the records. Thanks!
Yes holograms can be pressed into plastic but you'd have to make a negative of the hologram. Holocraft does not generate the animated circular ones like the one in the image above which uses the specular glints of reflected light as a means of animating the light as the record rotates, rather than producing a stereoscopic 3D effect - which is the intention of the holograms Holocraft generates.
The important thing to keep in mind is that the grooves formed by any metal dies pressed into the lacquer will need to have glossy smooth surface that results, to maximize the sharpness of the glinted light so it's not a blur along the groove (which produces a blurry hologram).
Ah thanks so much...any idea how the example you attached was created?
I don't know for a fact but it basically is just carving circles around the record (or impressioning them in) and offsetting their centers and radii to generate specular vertices. The 3D shape's rotation becomes automatic as the record rotates. It might be something as simple as just positioning the center of each vertice's circular groove where you want it to appear in 2D, which is to say that all of the circles are around the center of the vinyl and then you offset their centers to position their light glints in different places.
So for 4 points that are the corners of a square you would have four circles with matching radii and just offset their centers a bit. If you want a 1" square then you offset each one by 0.5" in the X/Y to represent the four corners. When you light that up you'll have four glints and when you spin the record the four glints will appear to rotate in-place.
EDIT: I'm not sure you need to vary the radii of the circles at all, it would change the apparent depth of the glints but I don't think it's necessary to produce the animated/rotating model effect.
I know you said lasers are not ideal, but since you can do this with a hand scribing tool, I imagine it's possible. Is it possible to get a vector file to play with? Something that would support a 0.005-0.07 spot size? Those are the lasers I have, but a fiber laser would be 1/10th that size, and can mark metal, so that seems like it has even more potential.
If you can get the laser to produce a reflective surface within the groove it should work. The ideal tool is something conical with a very tiny radius at the tip, something like 0.002" so that there's a nice concave and self-polished surface within there. There are two sample/example G-codes generated from Holocraft that you could try. They are identical in terms of the hologram they produce but one uses strictly G1 feed commands while the other utilizes arc-feeds instead (someone was curious about the difference so I created these to show them).
Here's the links to the G-code produced:
Hologram Segments
Hologram Arcs
Let me know if an SVG of the groove optics would be better than G-code for you to test out. I'd love to see what kind of results you can manage w/ a laser :)
Yes, I would prefer an SVG. My laser can import vector files directly. It supports G-code, but I've never used that so I don't know how.
Alright, here's a re-creation of the other hologram that I linked to the G-code for. There's two versions, one that is made up of line-segments, and one that is made up using SVG's native cubic bezier curves.
Hologram Segments SVG
Hologram Curves SVG
Keep me posted!
Any discoveries to share creating specular holograms using a laser?
I tried clear acrylic, it didn't work... I'm not sure if black acrylic would work better, or if it's the same. But I was using extruded acrylic as it wouldn't frost to white when engraved, and I don't have any extruded black handy.
Thanks!
Hi, I bought Holocraft a while ago, how can I get the latest update?
If you're logged into itch.io (which you should be if you're able to post to this messageboard) then there should be a bar visible at the top of the Holocraft page that is captioned with "You own this tool" and a download button that will show you the current downloads owners have access to. This is what it should look like:
Just wondering if you got around to fixing the texture feature yet?
Sorry about that, I've been very busy with PixelCNC. I'll make it a point to get the texture function running in Holocraft once PixelCNC v1.41a is out the door. It should be done over the coming week or two. I'm currently hacking away at adding DXF import support, and it's a bit of a tricky format, but once it's in there I'll dive back into the Holocraft codebase and get that all squared away for ya. :)
Any new holograms to show off?
Thanks sounds good. No havent made any new ones. I've moved twice in this last year so it's been busy. I'll let you know though as soon is I get everything up and running again.
Finally released PixelCNC v1.41a. I'm working on Holocraft's texture feature now. Should have an update released in the next few days!
Sounds good
Had texture mode working about a week ago, but spent time tweaking and tuning everything else (as one does). v2.3a is up!
Greetings. Could you post an example of the CNC-code that produces Holocraft (about 30-50 lines)?
Sure thing! Here's the example hologram as depicted in Holocraft itself:
Here's the hologram output with grooves articulated as linear feed motions:
http://www.deftware.org/Holocraft/hologram_segs.txt
...and the same hologram output with grooves comprising chains of circular arc feed movements:
http://www.deftware.org/Holocraft/hologram_arcs.txt
Thanks for the answer. This type of G-code suits for me (for converting to Heidenhain format).
Great app. I bought it.
Great! Thanks for your support :)
Feel free to let me know if you have any ideas/suggestions.
Hi there,
I was just wondering, which specific type and thickness of aluminum do you use for making these holograms? I saw you mention McMaster-Carr as a supplier. Additionally, would it be possible to achieve a similar effect on different metals like stainless steel, copper, or brass?
And lastly, which plastic yields the best results for this method?
Thank you,
Robert
The thinner the aluminum the cheaper - you just don't want something that will be super flimsy and unwieldy. The situation with aluminum is that it's highly reflective compared to other metals, insofar as the percentage of the spectrum that it reflects. It is only out-shined by silver, so maybe silver-plating an aluminum hologram would be a good way to really shine it up. In my experience just polishing up the face of a freshly cut hologram with a rag and some polishing compound can just about double the brightness of the hologram's groove optics and thus the hologram itself.
Aluminum is also pretty soft compared to other metals and lends itself well to having the optics scored into it just by dragging a hard implement over its surface like carbide/diamond. I'm sure other metals will work to some extent, but will be harder to cut and also not as brightly reflective as the grooves will not form as easily, depending on how hard the metal is, and may come out with a rough finish that doesn't reflect light as a nice little glint from one spot.
I have not yet used any plastics but I know that holograms can be made which instead of reflecting light off the face of the hologram they instead refract it from the backside of the hologram. Not sure Holocraft is yet up to the task without spending a day of adding some modifications to code - but it's worth experimenting and looking into.
Plastics may require some finesse, however. I'm sure that reflective specular holograms can be made from dark glossy plastics but I have no experience with making holograms from plastic that yields acceptable results. Maybe coating the plastic afterwards. There's not really an easy way to polish up the plastic without marring it's gloss - not like with aluminum where you can just buff it up with a rag and have all the groove optics become much shiner. Maybe fume polishing?
Also, there's another aluminum supplier that always has 15% off sales (or thereabouts) just sign up for their mailing list. Their prices are competitive with McMaster-Carr: www.onlinemetals.com - 0.025" 5052-H32 Aluminum Sheet I usually go with 1100 or 3003 alloys because they're more pure, and thus softer/shiner but 5052 is pretty cheap right now and is equally as soft and only slightly less pure. Having followed aluminum prices over the last few years: less than $3.50 for a 12"x12" sheet is a really good deal! I wouldn't pass it up if I were actively making holograms.
Thanks for the questions!
Charlie
That sounds great! Do you also have any suggestions for (or a link to) a specific diamond or carbide drag bit that you have used that works well?
And if so, do you have recommended feed and speed values, or is that controlled by / built into the software itself?
Thanks!
Robert
Speed should be zero: no spindle needed. Feed should be as fast as you can go without inducing wobbles into your grooves - this was the problem I had to fight with my machine because it just has too much flex. If you try to mitigate it by using a slow feed rate the hologram not only takes forever to make but also the grooves don't come out as smooth and shiny. There's something about pushing aluminum out of the way quickly that results in much more reflective grooves.
I fashioned hologram bits from pyramidal carbide engraving bits, by carefully rounding the point into a tiny hemisphere that I can only barely make out with a loupe. I haven't used a diamond-drag bit but I imagine it would work if it's not a super fine point and/or if you minimize the pressure/depth.
Actually getting good groove optics to form is a bit of a trial-error process that may take a few tries to figure out. Holocraft assumes a round tool and takes in a diameter to generate an optimal depth below the surface of the hologram to press into it. The actual value doesn't have to be exact, just experiment and find what works. Holocraft also varies the depth based on the assumed light altitude angle, to maximize the reflectivity of the groove for a spherical cutter. I think I might replace all this behavior with just a user-entered "cut depth" value instead.
Charlie
Dear Deftware,
Thanks for your latest very well explained response.
Are the files that we get with your software vector or raster files?
A few more questions:
1.- Can I get with a CNC depths of around 3 microns?
2.- Can you recommend a CNC?
Best regards,
Dan
Holocraft outputs SVG vector-image files, and then also simple mach3 compatible G-code.
Only an industrial CNC on the high-end of the cost spectrum will be able to get close to 3 microns, and only if the person running it has years of experience and background knowledge about machining works, let alone CNC machining. Some of the CNCs on the cheaper end of the spectrum (~$50k) will easily hold a few thousandths of an inch, but if the person running it knows what they're doing I've seen parts holding about 0.001" all day. To get 10x smaller you'll need a machine that's 10x more expensive, at the very least, with cooled ballscrews and spindles to mitigate thermal distortion.
I only have experience with Haas CNC lathes and mills, and much less running a few other older machines from the 80s as a button-pusher when I was younger, and then with my own hobby tabletop build running on an Arduino that I'd like to rebuild the mechanics of someday.
Can I ask what you're planning to do with a machine that precise? Industries that require the best possible precision, only because nothing less will do for the application at hand, tend to be the ones that buy these kinds of CNCs. For most serious industrial applications anything that can be made to hold just a thousandth of an inch is sufficient (and more affordable!)
Dear Deftware,
Thanks for your response. Today I bought your software but I still need to buy either a CNC or laser engraver; can you recommend some options as I am not familiar with either one? I think that I would like more a laser engraver?
Also with your experience what will be the minimun depth of a scratch that I can attain?
best regards,
Dan
Hi Dan,
The laser engraver isn't going to be sufficient for producing the optic grooves for specular holograms. You're going to want a rigid CNC - and the larger the tabletop type CNC the less rigid it will be (unless it's designed to be large *and* rigid). The reason is that it's difficult to get optic grooves to form that aren't wobbly if the machine isn't as rigid as possible. You want to use something like a diamond-drag bit, or a carefully rounded carbide point that you can score your plastic or aluminum with to produce optics. Plus, if you get a CNC you can make other stuff too! A laser engraver will only be able to do so much, by comparison, even though it can do some things that a CNC router/mill wouldn't be able to do - or do easily.
The minimum depth optics you can produce can easily be 0.001-0.003" deep but the real question is how wide they are. The wider the optics the less you can fit into your hologram before they start overlapping and degrading one-another whenever they find themselves densely packed into an area. It's a fine balance between minimizing the number of optics to reduce interference (it's OK if you have some that intersect eachother but not a whole bunch cross-crossing all over the place which ruins their ability to reflect the light source) while also having enough optics to convey the geometry in question.
Watch out for creating holograms will too many optics - it can take a long time for Holocraft to output your SVG/G-code (especially if you have occlusion detection enabled) so you want either simple geometry or to take a complex model and devise a way to visually convey it to viewers using the fewest number of optics possible. It's very easy to over-do it.
The other trick is making the hologram as big as possible - which means having a machine that's big enough to fit your hologram material into that you want to score the groove optics into while not being so big and flimsy that the optics come out all wobbly. Playing with feed rate and adjusting cutter diameter to control the groove depth can have a big impact on whether or not resonant frequencies are generated while optics are formed. Optics also come out more reflective if you run your machine as fast as possible - trying to mitigate the speed wobbles by running it with a slow feed rate will not only take forever to produce a hologram but also produce grooves that are not very optically reflective.
Hi Deftware,
My intention is to create high resolution images that will measure between 1 x 1 inches to no more than 6 x 6 inches. The images will be 3D and also 2D and some if possible like Matthew Brand type of images. I am looking forward to creating really nice and well defined images. Today I am buying the Holocraft program, do I also need the Pixel CNC program?
Thank you for your support! PixelCNC is useful for conventional routing/milling/engraving/signmaking/art but is not needed for making specular holograms using Holocraft. Holocraft only outputs basic Mach3 type G-code, otherwise you can directly output SVG of your specular hologram optics and generate G-code from that yourself using a different CAM type program (PixelCNC currently doesn't convert SVG paths into toolpath G-code). Using the built-in G-code generator in Holocraft is the most convenient if you're able to use its output with your machine, however. When exporting G-code set your tool diameter very small ~0.002, and set depth-per-pass at any number higher than that ( tool diameter is what determines how deep the optics are, which you can see as "Groove Depth" on the bottom left of the G-code export dialog ). Inches Scale determines the size of your hologram, specifically the black square area around your optics in the 3D view. Safety Z is how high the cutter will retract from the Z0. surface to move to the next optic to be scored. Origin at center outputs G-code that assumes you've zeroed out your CNC machine in the absolute center of your hologram material/workpiece, otherwise it will output G-code that assumes the front-left corner of your material is the XYZ origin (i.e. coordinate 0,0,0) I'd suggest outputting circular arcs instead of linear segments, it will be much smoother and more compact, though you may want to also reduce the precision value on the top-right a bit to adjust how many arcs are output per optic. Let me know if you have any other questions. Thanks!
Hi Deftware, based on the last comment of 7 months ago do you sell a pixel CNC system?
Hi Deftware, I would like to buy your software but can you recommend a not too expensive CNC or laser engraving systems?
Hi Nanografix,
It depends on what you'd like to be able to accomplish. Some machines are better for signmaking because they're bigger without much Z-travel while others are better for engraving and/or milling more precise parts because they're smaller and more rigid. What do you plan to do?
Hey I have a question. I was thinking of buying your pixel cnc, do you plan on integrating any rotational axis like a, b, or c. I ask because I'm building a 5 axis cnc and I like the look of your program.
Thanks! I do have a hankering for some 5-axis toolpath generation algorithm work at some point down the road, but PixelCNC is not the project that I will be tackling 5-axes with.
PixelCNC's primary focus is on loading 2D images as input (although v1.30a will be released today which includes 3D model import functionality, but that just generates a 2D image from the 3D model geometry). As a consequence of the 2D image paradigm the complexity of a project never necessitates more than 3-axes of cutter articulation - with the exception of projects that may have deep spots where a tool is not long enough to reach a cut from a vertical approach, and the chuck will crash into the material.
Otherwise, as long as the cutting tool is long enough to prevent the spindle from crashing into the material a 3-axis will always be able to do anything PixelCNC is capable of generating simply because every surface of a PixelCNC project is accessible from directly above it. There are never overhangs or undercuts, etc.. This is just the nature of 2D heightfields, which is effectively PixelCNC's core premise.
In either case, there's no reason you can't run 3-axis programs on a 5-axis CNC! :)
Just wondering how things are progressing on the texture feature :)
3 in on stainless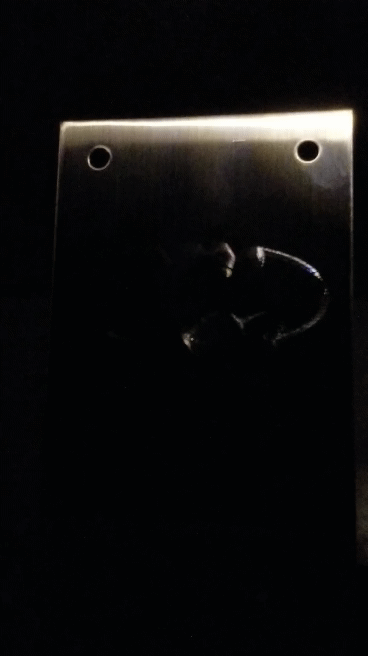
Not bad! Thanks for sharing :D
I talked to Matthew Brand and he offered me some tips. Let me know if your interested I'll send you what he told me.
Sure, that would be great. I sent him an email twice, about 6 months apart, but never got any reply.
He told me "
* I use a fairly massive CNC machine to drag a diamond stylus through aluminum alloy at a depths of 20-50 micron. Had to customize some machine parts and programming to get optically smooth motion.
* It helps to tilt the stylus slightly in the direction of motion and to use a very light-gauge lubricant. I grind & polish the stylus to a Rouleax-like shape to promote reflectivity.
* Everybody gets the geometry of the stylus motion curves wrong — they're not conic. You need to solve an ODE that asks for rigid 3D image motion when some part of the optical path (e.g. the plate) moves.
* Lighting should be consistent with whatever assumptions you make in your ODE. Point-like sources work best; broad-spectrum sources allow diffractive color effects."
Hope this helps
Right now the square that you setup your hologram scene within is what you set the size of via the export dialogs:
The blue arrows are the extent of your hologram, so you want to keep your optics within there if you're doing a square hologram. Otherwise, if you can extend your hologram horizontally further if you wish, and let your optics overlap into the MARGIN areas. The blue rectangle around the 'Inches Scale' CNC export parameter refers to the length of the arrows denoting the hologram's size, in inches.
Since you set the size of the hologram at export time all you need to worry about is keeping things inside the square, but there's not currently a way to specify a size ahead of time: the hologram-area square has no actual size, so there's nothing for rulers to show if they were there. But, if you want to make a non-square hologram that's wider than it is tall, then just keep all your optics within the top/bottom of the window, vertically, and let your optics extend out into the margins a bit, and then the Inches Scale parameter would just be referring solely to the height of your hologram. Keep in mind though that if you're not using 'Origin at Center' that the bottom-left of your hologram will only be for the square area. A rectangular hologram will not start at the actual bottom-left most corner of your hologram's optics. I personally recommend you use the center origin mode, and then measure the center of your material to zero your CNC at.
I've been trying to hack in a bunch of little things real quick into v2.2a before I upload it, while I have the time today. I'm starting to feel like I should expand Holocraft's model-loading capacity, because right now it's limited to very simple models with low vertex/polygon counts - due to the data structures it precalculates from the model to facilitate fast optic generation. I'm also going to separate the optics slider into two sliders: optic count and threshold, so that if you are in Vertex or Wireframe mode you can adjust the number of optics to squeeze onto a edge line while independently adjusting the threshold at which an edge line qualifies for having any optics created along it at all.
Right now I'm switching over to 64-bit compiler to allow Holocraft to allocate more memory and be able to load larger models (~4x more verts/polys), due to 64-bit EXEs being able to access tons more system memory. I've also changed Holocraft to allocate memory dynamically.
There's some weird thing going on where some models have more than two polygons attached to a single edge spanning two vertices. If I can figure out how to resolve these funky situations (or a model having 50+ polygons to one single vertex!) I can expand it pretty easily to allow for much more complicated models.
Your hologram looks pretty good so far, but I do have some pointers. It looks like your light angle doesn't match the actual incident light angle. The light source's angle changes the 'depth' of the hologram, as far as how much straight above the hologram it's shining in from. You can tell if your light is too high and not out in front of the hologram enough because the object rotates much faster/farther than the actual hologram surface itself. You want to match your light position with what you have your Light slider set to. This changes the vertical steepness of the optic grooves themselves to match the light source, and the holographic effect is much more pronounced when the viewer orientation (or hologram angle) matches the apparent orientation of the geometry being depicted.
Also, if you can find some kind of metal polish (I use one called 'Blue Magic') and put a bit onto a rag, and then just buff the whole surface of the hologram real quick after cutting it you can shine up your grooves and double their brightness really easy. You don't need to buff the whole thing to a mirror shine, just going over it with a rag and some metal polish real quick will clean them up and get brighter glints.
For cutting I took some little pyramid carbide engraving bits (they look like a 3-sided pyramid at the tip, but have a tiny trangle facet on the very tip where the 3 sides meet) and diamond-ground it into more of a very slightly rounded point - getting rid of that triangle facet. A rounded point will produce rounded grooves which can catch the light at almost any angle, maximizing your glints. This took me a bit of trial/error to get right, but basically I just ground the carbide to a point by spinning it in my spindle and put the diamond grinding surface on it. Once it was a sharp point then I just barely rounded it by tilting the diamond sharpener up and over to the opposite side once or twice. You want a super duper tiny diameter.
One last thing: you want to figure out what feed rate minimizes any wobbles you get in your optic grooves. A bunch of pressure and moving too fast or slow on a machine that has some flex can induce little speed-wobbles in the tool as it scores the surface, which produces 'blurry' looking holograms that don't have nice sharp defined glints - because the glints will appear all over the optic in multiple spots.
I'll have v2.2a up within a few hours. I almost want to get some more aluminum sheets and start making bigger holograms now! Maybe I'll throw a few bucks at McMaster Carr as a holiday splurge and see what I can make happen over vacation.
Love the update
Good to hear! I'll probably hammer out a few more things soon, no telling when, but hopefully within the next few weeks. I'd like to add better multithreading capability to speed up rendering and optic generation - it would be nice if loading bigger models didn't bog it down as much. I'm also thinking about modifying it so that when you are rotating/moving the model around it draws a low-poly proxy so that it's responsive.
More importantly I'd like to add better optic generation, maybe one that is sort of the inverse of the vertex mode - where it plots optics at the centers of polygon faces? I'd like to also make the wireframe optic mode have shading like the vertex mode has now. The big feature I got running a bit in the old version of Holocraft, pre-2.0, with the projected texture optic generation is something I'd like to get going as well, so that you can just have an arbitrary pattern of optics across a model, regardless of its vertices and polygons.
Right now I'm working on a devlog post for this release.
I think I've got my scratching technique down. I'm using an auto center punch to keep it contact at the correct pressure to make I light scratch.
How does the Texture work exactly? When I click load texture nothing happens.
The texture mode actually isn't implemented yet. It is implemented in v1.3a, however, and simply allows you to load an image *which is 'projected' onto the loaded model as if there's a slide projector casting the image onto the model from your vantage point, and light pixels in the image translate to creating optics while dark areas are blank. This gives a sort of raw control over how optics are distributed over the surface, instead of relying on how a model's vertices or polygons/edges are situated. I will try to get it all running by the next version ;)
Thanks for an awesome program
I'm glad Holocraft is finding some use! :)
I'm releasing v2.2 right now to fix an issue with how text is output for both SVG and CNC g-code that causes new-line/carriage-returns to be output wrong at times. I'm also including some example models with the build, so users can start playing with some geometry. I'd like to improve the optic placement/generation, and finally get texture mode in there so that an image can be 'projected' onto a model and used for designating where optics should be across its surface, so that any geometry can be depicted instead of by its vertices or edges - which can sometimes not be very good for generating optics off of with some models.
What does it mean when it says optic segments overflow and crashes?
Also how do you get it to not calculate the back of the object through the front? Like its transparent.
Hi
nramconracmo, (woops!)Optic segments overflow means that an optic is being broken up into more than 24 individual occluded/unoccluded segments, where you can think of an entire optic depicting a point in 3D space and the length of the optic is broken into "visible" and "invisible" sections. If you have a model of say a triangle way in the background and then a set of 20 vertical rectangles that make parts of it visible and invisible all along the viewing angle then its optic segments will get broken up too much.
Also, it's recommended that you disable 'Intersection Resolution', which can also cause a segment to be chopped up into too many segments. It was more of an experimental feature but I have yet to get it working as good as I was originally hoping, and it's best to leave it disabled.
Your resulting hologram should be 'opaque' as long as 'Occlusion Detection' is enabled. This will prevent optics from being created for back-facing geometry, and also clip sections of optics that are blocked from view by foreground geometry. If you also want it to appear completely opaque in the view you can enable 'Show Faces' in the View menu.
Also, I don't recall if it's mentioned anywhere, but the 'Light' slider controls the expected/assumed azimuth (pitch angle) of the illumination source, where when the slider is at the top-most position the light source is assumed to be directly above the hologram, shining down on it at a 90 degree angle from the direction the hologram is facing. At the bottom of the Light azimuth slider is 60 degrees, so still from somewhat above the hologram but shining more 'head-on'.
The purpose is to accomodate the use of a ceiling light source in different sized rooms, where a larger room with a lower ceiling would use a Light angle that has the slider closer toward the bottom, and a room with a light more directly above the desired hologram position will have the slider up higher.
Also, if you have any requests or ideas for features I'd be glad to hear them! I am pretty busy working on PixelCNC most of the time but I am always willing to see what I can do. If there's a limitation or a bug that you would like me to look at, or a feature or change, just let me know!
There is a problem with the svg file conversion.
(empty file or program no response...)
Please add conversion function to dxf file.
I will look into it.
Seems to be working fine:
Holocraft does not "convert" models to SVG, it generates groove optics from a model, which can be output as SVG lines/arcs/curves or as Mach3 CNC G-code, but it's up to the user's discretion how optics are generated: the perspective of the model, which metric to generate optics by, etc.
Are you creating any optics? Are you saving the file to a location that doesn't require administrator privileges? Now that PixelCNC has reached a relatively solid and decently featured state I was going to change gears to start making videos to demonstrate it and show off its capabilities, perhaps it would be a good idea to make a Holocraft tutorial video as well.
Also: what settings are you using on the SVG output settings dialog?
What if I hire you in order to develop this further?
Dan Lieberman?
Hey is it ready to buy it the sofware?
Please contact me Lucasbeathyate@gmail.com! Thnx´s!
Dear Mr. Van Nuland,
Are you selling a complete solution? If not can I buy the Holocraft software?
Best regards,
Dan
Danl@nanografix.com
You can buy Holocraft now, but its development, documentation, and support are low-priority for the moment. It has been released purely to satisfy the curiosity of the most courageous. Thanks for your interest.
Hola! estoy interesado en obtener el programa, estoy terminando una muestra artistica en Uruguay. Y me gustaría exponer algunas obras con estas caracteristicas, obviamente con los respectivos creditos a los desarrolladores del programa lucasbeathyate@gmail.com es mi mail
This looks amazing! Is there any way to download / purchase Holocraft? I'd LOVE to play around with it!
Thanks!
Hi, apologies for the delay in reply. I'm not currently offering Holocraft for sale to the public yet as it is destined to become a facet of a final CAD/CAM package for DIY hobby CNCer's. If someone only wants Holocraft then that's the only 'option' they are charged for (along with the base CAD/CAM program fee). There will be a variety of optional features users can pay for, so they're not forced to shell out a few hundred bucks just for 1 or 2 features that they might use in existing programs.
You can buy Holocraft now, but its development, documentation, and support are low-priority for the moment. It has been released purely to satisfy the curiosity of the most courageous. Thanks for your interest.
Hi,
What if I hire you in order to develop this further?
Best regards,
Dan Lieberman
CEO
Hey, is this software available for download yet? It looks incredible and I'd love to use it to make some holograms. Thanks, Sarah
saziz@artic.edu
You can buy Holocraft now, but its development, documentation, and support are low-priority for the moment. It has been released purely to satisfy the curiosity of the most courageous. Thanks for your interest.